硬質合金刀片CVD塗層工藝
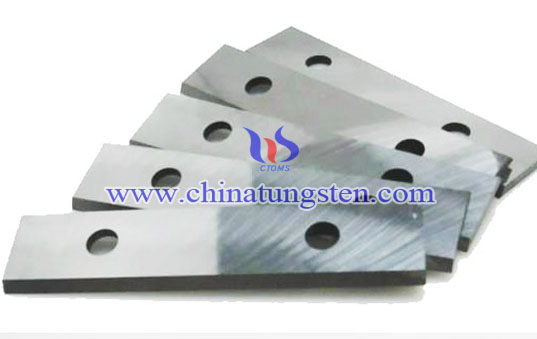
目前硬質合金刀片CVD塗層工藝中較普遍的塗層結構是:氮化鈦-氧化鋁–氮碳化鈦–基體。碳化鈦塗層具有很高的硬度與耐磨性,抗氧化性也好,硬質合金刀片切削的時能產生氧化鈦薄膜,降低摩擦係數,減少刀具磨損。一般硬質合金刀片的切削速度可以提高40%左右,碳化鈦與鋼的粘結溫度高,表面晶粒較細,硬質合金刀片切削的時候很少會產生積屑瘤,適合於精車。碳化鈦塗層的缺點就是線膨脹係數與基體差別較大,與基體之間形成脆弱的脫碳層降低了刀具的抗彎強度。因此,在重切削、加工硬材料或帶夾雜物的工件時塗層容易崩裂。
氮化鈦塗層在高溫時能形成氧化膜,抗粘結性能好能有效地降低切削溫度。氮化鈦塗層刀片抗月牙窪及後刀面磨損能力比碳化鈦塗層刀片強。適合用於硬質合金刀片切削鋼與粘刀的材料,加工表面粗糙度較小,硬質合金刀具的使用壽命較高。此外氮化鈦塗層的抗熱振性能也較好,缺點是與基體結合強度不及碳化鈦塗層且塗層厚時易剝落。
硬質合金塗層最常用的方法是高溫化學氣相沉積法(簡稱HTCVD法),是在常壓或負壓的沉積系統中,將純淨的H2、CH4、N2、TiCl4、AlCl3、CO2等氣體或蒸氣,按沉積物的成分,將其中的有關氣體,按一定配比均勻混合,依次塗到一定溫度(一般為1000℃~1050℃)的硬質合金刀片表面,即在刀片表面沉積TiC、TiN、Ti(C,N)或Al2O3或它們的複合塗層。 用PCVD(等離子體化學氣相沉積)法在硬質合金刀片表面進行塗層也得到應用,因塗層工藝溫度較低(700°~800°),故刀片的抗彎強度降低的幅度較小,對銑刀片比較適宜。
塗層前,基體刀片表面須淨化,切削刃部位應鈍化。塗層後,因塗層材料與基休材料的線膨脹係數存在差異,故塗層刀片表面不可避免地產生殘餘張應力而使刀片抗彎強度降低。通常用TiC薄層先塗在基體表面上,因TiC的線膨脹係數與基體材料最接近;外面再塗TiN、Al2O3等。過去,單塗層材料均用TiC,雙層塗層材料多用TiC/TiN、TiC/Al2O3等,三層塗層材料多用TiC/Ti(C,N)/TiN、Tic/Al2O3/TiN等。近年,隨著基體材料的改進,塗層材料也有用TiN墊底的,即TiN/TiC/TiN等塗層材料還有HfN、MoS2等。