硬质合金刀片CVD涂层工艺
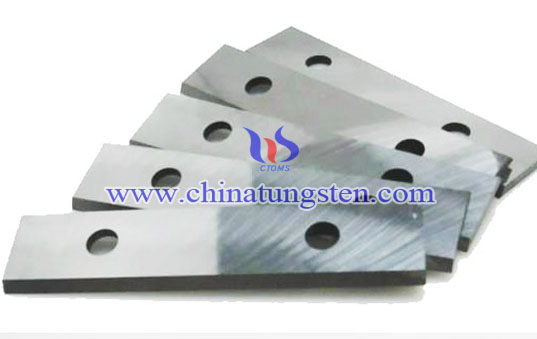
目前硬质合金刀片CVD涂层工艺中较普遍的涂层结构是:氮化钛-氧化铝–氮碳化钛–基体。碳化钛涂层具有很高的硬度与耐磨性,抗氧化性也好,硬质合金刀片切削的时能产生氧化钛薄膜,降低摩擦系数,减少刀具磨损。一般硬质合金刀片的切削速度可以提高40%左右,碳化钛与钢的粘结温度高,表面晶粒较细,硬质合金刀片切削的时候很少会产生积屑瘤,适合于精车。碳化钛涂层的缺点就是线膨胀系数与基体差别较大,与基体之间形成脆弱的脱碳层降低了刀具的抗弯强度。因此,在重切削、加工硬材料或带夹杂物的工件时涂层容易崩裂。
氮化钛涂层在高温时能形成氧化膜,抗粘结性能好能有效地降低切削温度。氮化钛涂层刀片抗月牙洼及后刀面磨损能力比碳化钛涂层刀片强。适合用于硬质合金刀片切削钢与粘刀的材料,加工表面粗糙度较小,硬质合金刀具的使用寿命较高。此外氮化钛涂层的抗热振性能也较好,缺点是与基体结合强度不及碳化钛涂层且涂层厚时易剥落。
硬质合金涂层最常用的方法是高温化学气相沉积法(简称HTCVD法),是在常压或负压的沉积系统中,将纯净的H2、CH4、N2、TiCl4、AlCl3、CO2等气体或蒸气,按沉积物的成分,将其中的有关气体,按一定配比均匀混合,依次涂到一定温度(一般为1000℃~1050℃)的硬质合金刀片表面,即在刀片表面沉积TiC、TiN、Ti(C,N)或Al2O3或它们的复合涂层。 用PCVD(等离子体化学气相沉积)法在硬质合金刀片表面进行涂层也得到应用,因涂层工艺温度较低(700°~800°),故刀片的抗弯强度降低的幅度较小,对铣刀片比较适宜。
涂层前,基体刀片表面须净化,切削刃部位应钝化。涂层后,因涂层材料与基休材料的线膨胀系数存在差异,故涂层刀片表面不可避免地产生残余张应力而使刀片抗弯强度降低。通常用TiC薄层先涂在基体表面上,因TiC的线膨胀系数与基体材料最接近;外面再涂TiN、Al2O3等。过去,单涂层材料均用TiC,双层涂层材料多用TiC/TiN、TiC/Al2O3等,三层涂层材料多用TiC/Ti(C,N)/TiN、Tic/Al2O3/TiN等。近年,随着基体材料的改进,涂层材料也有用TiN垫底的,即TiN/TiC/TiN等涂层材料还有HfN、MoS2等。