Tungsten Carbide Welding Blades
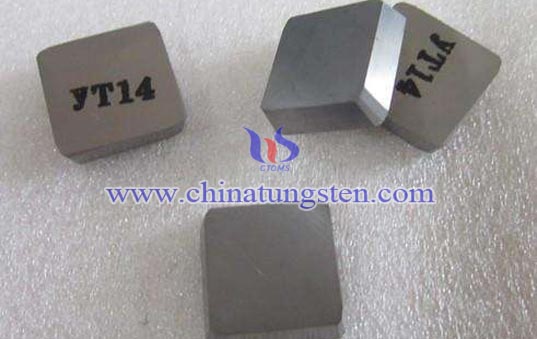
Tungsten carbide welding blade using finer than the raw powder YG6 and YG8 ensure product abrasion resistance, cast iron and nonferrous metal finishing and semi-finishing of choice. Its wear resistance and allows higher cutting speed YG6 and YG8. tungsten carbide blades for welding steel and stainless steel processing characteristics, the scientific selection of alloy composition and structure, supplemented by the production process optimization, make better universal properties of the alloy, the scope is wider, can be used for steel, stainless steel, semi-finishing and light load roughing; selection of quality ultrafine tungsten carbide powder, so that the wear resistance, impact resistance, thermal shock resistance, good combination. tungsten carbide welding blade for cast iron, nonferrous metals, heat-resistant metals, semi-finished titanium alloys, high impact resistance, the need for continuous and broken cutting.
Key points of tungsten carbide welding blades:
1、Welding cutting tool structure should have sufficient rigidity 2、Tungsten carbide blade should be fixed firmly |
![]() |
3、carefully check Arbor
Before the blade welded to the shank of the blade needs, Arbor carry out the necessary checks, first check the blade bearing surface can not have a serious bent. Carbide welding surface may not have serious carburized layer, should also be Carbide Arbor blade surface and dirt tank inserts were cleared to ensure the welding firm.
4、Rational use of solder
In order to ensure the welding strength, you should choose a suitable solder in the soldering process, should ensure good wetting and liquidity, and the exclusion of air bubbles, making welding and alloy welding face full contact, no shortage of welding phenomenon.
5、the correct choice of welding flux
Recommended industrial borax, dehydration should be treated prior to use in the oven, and then crushed and sieved to remove mechanical impurities and set aside.
6、the compensation selection mesh gasket
When welding high-low cobalt fine particles of titanium alloy and alloy welding long, thin blade, to reduce welding stresses, recommended thickness 0.2--0.5mm sheet or mesh aperture of mesh welding compensation gasket 2--3mm .
7、the proper use of sharpening method
Because tungsten carbide blade brittle, crack formation susceptibility strong, so the tool sharpening process should avoid overheating or quench, but also to choose the right size of the wheel and reasonable grinding process, avoid grinding cracks, affect tool life.
8、the correct installation tool
When installing the tool, extending the length of knife blade should be as small as possible, otherwise easily lead to tool vibration, thereby damaging the alloy film. p>
9、right regrinding, grinding tool
Use the tool to normal blunt, must be re-grinding, tool regrinding after, be sure to use stone for edge and corner radius grinding, this will improve the life and the safety and reliability of the tool.